本篇文章内容由[中国幕墙网]编辑部整理发布:
前言
随着科学技术的发展、资源和能源的日益紧张,环保意识的不断加强以及产业重心的转移和优化重组,铝型材(词条“铝型材”由行业大百科提供)产业加工装备向着短流程、高效率、精密化、自动化、大型化方向发展;生产工艺向则向低能耗、低污染、绿色环保方向发展;产品向着高强度、高稳定、高性能、高附加值、多功能、多用途方面发展。
在铝合金型材(词条“铝合金型材”由行业大百科提供)阳极氧化(词条“阳极氧化”由行业大百科提供)表面处理工序中,碱蚀为一重要处理工艺,以去除天然氧化膜及型材表面轻微划痕,使型材裸露出均匀的、新鲜的、理想的表面,以利于进行阳极氧化。
生产中当碱蚀槽铝离子>35g/l时,槽液中的偏铝酸钠易发生水解(词条“水解”由行业大百科提供)而生成氢氧化铝沉淀、脱水、结块变硬,且与槽壁结合十分牢固,需经常停产清理。
一、碱蚀添加剂(词条“添加剂”由行业大百科提供)
针对偏铝酸钠的不稳定性,碱蚀中加入有机酸钠盐,使铝离子与其产生络合作用而使NaAlO2 不发生或较少水解,使最初水解生成的Al(OH)3晶核微粒不长大,即使发生也是软沉淀而不是硬块。其主要成分常为多羟基酸钠盐,如葡萄糖酸钠、柠檬酸钠、酒石酸钠等;有的配方加入大量硝酸盐或亚硝酸盐,以提高表面光亮度,但产生氨氮污染;有的配方加入表面活性剂和增粘剂,以方便做碱砂,但产生大量淤泥;还有的加入一定量的缓蚀剂,以降低铝的损耗和碱的消耗。具有如下特点:
1、 碱蚀添加剂的槽液只能与高浓度的Al3+(100~150g/L)共存,碱液才与铝材发生均匀、缓蚀反应,达到整平作用,碱砂效果更好。
2、槽液粘度大、浓度高、温度高,生产中带出量较大,铝材的损耗一般在2.5~3%;生产中须不断补充液碱,以保持游离NaOH的浓度;
3、 带出大量铝离子只能经废水站处理,存在大量污泥和水质污染问题,污泥中的氢氧化铝较难回收。

碱蚀添加剂的碱槽 晶析法工艺的碱槽
二、晶析法碱回收
晶析法是根据偏铝酸钠的不稳定性,利用槽液中的Al(OH)3晶核(粒度在0.1微米左右),加速偏铝酸钠(NaAlO2)的水解,经沉淀、脱水将氢氧化铝回收,氢氧化钠溶液则回流到碱蚀槽再循环使用,节能环保。
碱回收为闭路循环生产装置,碱蚀槽中的总碱含量稳定,铝离子控制在28g/L左右,槽液成份相对稳定,晶析槽中的Al(OH)3晶核在配槽时一次性加入,在生产中抽取到晶析槽的碱液内含有大量NaAlO2,在晶析槽内晶核的影响下,也会析出部分Al(OH)3晶核,这样循环生产,无需再加入晶核。
1、碱蚀槽NaOH的再生、回收
1.1碱蚀时的化学反应式(a)
(a) 2AL + 2NaOH+2H2O 2NaALO2 + 3H2
1.2碱蚀晶析槽中的化学反应(b)
(b)NaALO2 + 2H2O AL(OH)3 + NaOH
2NaALO2 + 4H2O 2AL(OH)3 + 2NaOH
(a)+(b) 2AL+ 6H2O 2AL(OH)3 + 3H2
1.3碱液回收过程,总碱含量不变,游离碱升高,铝离子下降。(表1)
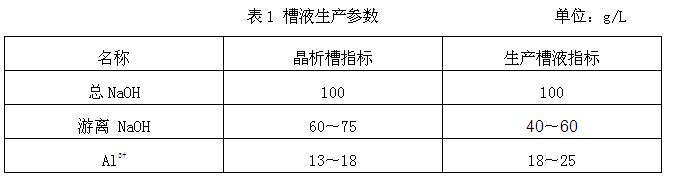
由表1可知,经分解后流回碱蚀槽的碱液浓度要高于流出的碱液浓度,这样可补充碱蚀过程NaOH的消耗,生产中只需补充铝材带走的碱量,有效降低了NaOH的损耗。铝离子也控制在28g/L以下,在此条件下生产的铝材表面质量稳定,相对一致。
2、碱槽中铝离子回收
当碱液中的Al3+达到28g/L(也即是NaALO2浓度高)时,将碱液抽到晶析槽内(已含有粒度在0.1微米左右的Al(OH)3晶核),经稀释、冷却、均速搅拌,促使碱液中的NaALO2分解,Al(OH)3沉淀物下沉到槽底,澄清的NaOH溶液溢流到回收桶,再抽回碱槽中循环使用;Al(OH)3浆液定期从晶析槽底部排出,用离心机洗涤脱水得到干状Al(OH)3 晶体,洗涤液抽回晶析槽。
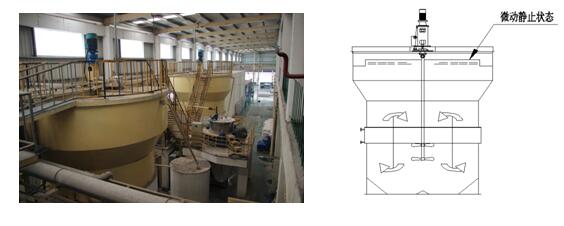
图1 晶析槽搅拌
3、 晶析槽维护
3.1 Al(OH)3浓度分析与脱离
将晶析槽底部阀门打开,流出2~3分钟后取样,静止45分钟后测量Al(OH)3浓度,当浆液Al(OH)3浓度在38%~40%,做Al(OH)3分离处理,脱水处理中需用清水清洗1~2分钟。 脱完渣后离心机应用清水清洗一遍。每隔15天左右要把滤布滤网拆下来清洗干净从新装上使用。
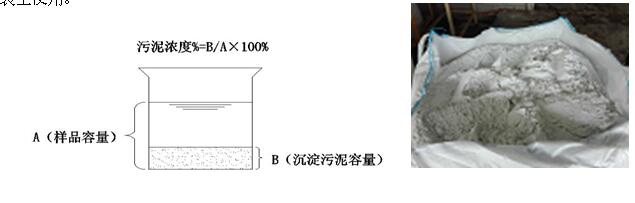
3.2晶析槽温度控制在40~45℃。当晶析槽温度达到44℃,把一半盖子打开,温度≥45℃,把全部盖子打开。正常情况下,内圈液位≥外圈液位,内圈槽液浑浊,外圈槽液澄清。
3.3晶析槽溢流沟要定期清理一次(视溢流沟污泥量多少而定):把软泥通过计量槽倒入晶析槽,硬泥不要,把它处理掉。晶析槽要定期查看有没有Al(OH)3污泥沉淀,当Al(OH)3污泥达到一定厚度时,就把它清理干净。
3.4晶析槽搅拌速度一般控制在550 r/min,碱液流出量控制在30 l/min以内,另外,搅拌机停止不能超过4小时,如需长时间停止维修,需用压缩空气搅拌;若搅拌机停止运转(停电)半小时以上,开机时需将转速提高,搅拌速度增加,运转2~3个小时后恢复正常的转速。
三、生产数据对比
3.1槽液成份
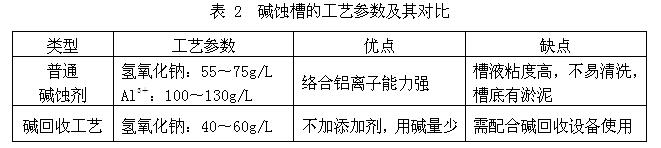
3.2化工损耗对比
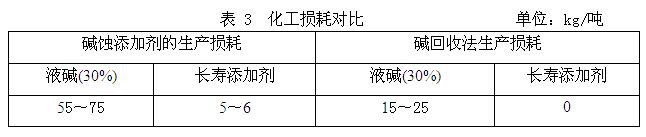
3.3铝离子的损耗
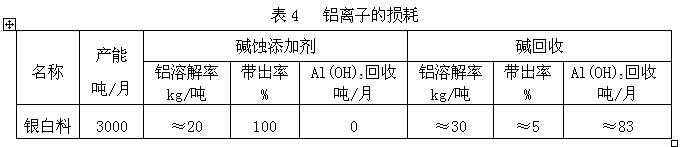
3.4废水处理
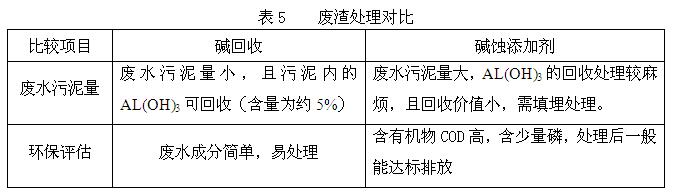
碱回收生产控制中,碱蚀液中的Al3+{Al(OH)3}可以得到有效回收,槽液中的Al3+去除率可达55%;每生产一吨银白料约可产生25~30kg的含水10~15% 的纯Al(OH)3,可有效地减少废水处理的污泥,达到防治污染的目的。
采用碱蚀回收设备,与加入碱蚀添加剂相比,碱液可再生、循环利用,液态NaOH(30%)损耗比加碱蚀添加剂约低70kg/吨,且槽液不加添加剂;晶析槽中的NaOH能大量回收重复利用,起到节能降耗的作用,且无有害物质产生。
结束语
采用碱蚀回收设备,前期投入较大,但生产中经晶析槽处理后的回流碱液浓度高于生产要求,可补充碱蚀过程NaOH的消耗,生产中只需补充铝材带走的碱量,液碱(30%)添加量为15~25kg/吨;回收的碱渣中氢氧化铝的含量高达90%以上,具有很大的经济效益,可加工成明矾、冰晶石、无机阻燃剂等。
从环境保护及生产成本来看,采取碱回收装置不仅具有明显的环境效益优势,且经济效益方面也具有很大发展前景。
参考文献
[1] 许旋,罗一帆《铝阳极氧化碱蚀槽的维护》
[2] 陈耿影,张志军《铝酸钠溶液中苛性碱全碱的自动分析》
[3] 朱祖芳《铝合金阳极氧化与表面处理技术》(第二版)
[4] 徐溢,徐斌 《含高铝高碱废液废渣分析及回收利用》