设计实例三,大型LED灯管(如图6)

基本参数:
挤压机吨位5000T,挤压筒直径?364mm,棒径?355,挤压系数17,模具直径:¢615
难点分析:该型材几何尺寸较大,直径达263mm,分为内外两层模芯,共17个空腔,形状复杂。一般情况下,这类结构的型材如果直径较小的话,生产难度不大,但是在直径较大的情况下,模具中心的挤压死区面积过大,造成挤压力升高,模具容易发生裂桥报废。考虑到上述难点,我们在经过详细的强度校核计算后,采用了上中下三层“模中模” 的设计结构,同时通过采用“前导孔”来降低挤压力,分流孔如图七所示。模具剖视图如图八所示。

“模中模结构”是较为少见的特殊模具结构,该结构可以使电火花的加工量大大减少,简化加工难度,缩缩短加工周期。我们所采用的“模中模”结构较好的解决了各个模芯位置的供料平衡问题,使模芯的受力达到平衡。型材各个部位的流速均匀,模具的应力分布状态得到极大改善,大大提高了模具使用寿命。上模和中模的分解结构如图九和图十所示。
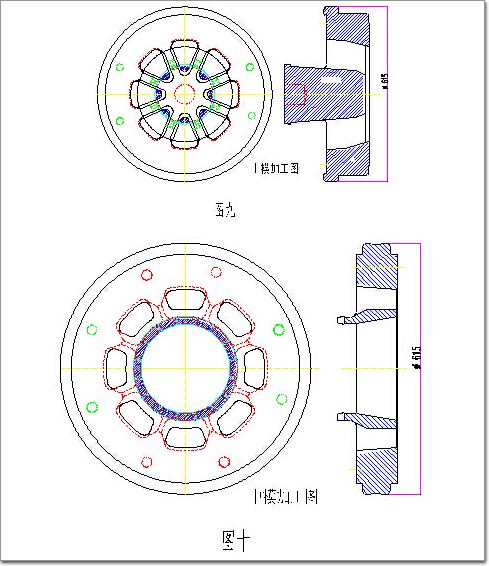
该模具上机后,出料情况理想,挤压力不高,料头整齐,壁厚较为均匀,但是螺丝孔处尺寸偏大,在经过修模调整后,该模具生产状况良好,成功生产出了合格产品。
设计实例四,大型复杂散热器(如图11所示)

基本参数:
挤压机吨位5000T,挤压筒直径?364mm,棒径?355mm,挤压系数17,模具直径:¢530mm.
难点分析:该散热器型材几何尺寸较大,并且有多处装配位,在齿上还分布有六个较小的空腔。从技术上看,该散热器型材的生产难度很大,主要问题是“偏齿”现象难以有效避免,在生产过程中,一旦发生偏齿现象,模具将很快报废。因此,该模具在设计过程中的核心问题是齿的受力平衡问题。
为了解决偏齿问题,我们在5000吨挤压机上,采用了九个分流孔的模具设计方案。为了降低挤压力,该方案同样采用了“前导孔”的结构设计,如图12所示。
从图中分流孔的布局以及型材在模具中的摆放位置来看,每个小公头在各个方向上均有不同的分流孔为其供料,使小公头在各个方向上的受力得到平衡和抵消。避免了公头偏壁现象,同时,各个散热齿在不同方向上的受力也通过分流孔得到平衡,避免了偏齿现象的发生。通过生产实践证明,该模具上机后出料平稳,料头整齐,各个散热齿的壁厚均匀,成型情况良好,生产出的产品完全满足客户的使用要求。
总结:
采用前导孔的模具结构能有效扩展金属在模具中的流动范围,金属在经过前导孔后,进行第一次宽展预变形,然后金属再进入上模分流孔进行第二次分流,金属在经过两次分配之后,模具的供料比例更为均匀合理,可以显著改善型材出料的成型度,前导孔结构由于增大了分流比,因此挤压力大幅降低,使模具的强度和稳定性都得到明显提高。在实际生产过程中,我们通过广泛使用前导孔的宽展模具,使挤压机的工作潜能得到充分发挥,减少了模具试模次数,尤其对于一些难度较大的型材,明显缩短了交货周期。
上一页12下一页